Home
My Work
How To
Opinion
Links
Camera
Photos
Friends
|
Examples of My Work
 |
Motorcycle suspension - The first version of my modified
1975 Hodaka. The stock rear suspension only had about 3" of travel,
while the Grand Prix bikes were running 6". I decided to modify
my bike for 7.5" of travel, so I cut the back of the bike off,
and built a new back section and modified the stock shocks by adding
a remote reservoir. I won my first race the first time I ran the bike.
I later cut the bike apart and rebuilt the suspension to use CZ air
shocks to get 13" of travel. I could jump anything wide-open.
|
Wood-working Lathe - I took machine shop in high school
and loved it. In 1974, for our end-of-year project , most guys were
making hammers, toy cannons and such. I wanted to make a wood-working
Lathe. The teacher told me it was impossible, but try it if I wanted.
A classmate and I build it in 5 weeks. It wasn't very good (the "ways"
flexed too much for deep cuts), but it did work and I got an "A".
It ended up in the school trophy case for years. Still have the drawings
somewhere. Never bothered to take pictures since I wasn't happy with
it. The teacher was Harry Paulin, and he was a really cool guy. Taught
me a lot.
|
 |
High Voltage Switchgear - My father taught me to design switchgear,
since he was in the business of building these. It involves sheet-metal
design and electrical design. We built a lot of custom equipment for
utilities all over the United States. This photo shows the front of
the equipment, with the power cables plugged into bushings, mounted
in a bulkhead. The bushings extend through the bulkhead to the back,
where fuses were mounted. I wasn't happy with the bushings and insulators
we could buy, so in 1979, I started Elliott Molding and Components to
design and build my own (next story).
|
 |
High Voltage Bushings - These are known as "Apparatus
Bushings " in the Electric Power Industry. They are used to connect
underground power cables to switchgear - large green enclosures that
contain switches, fuses and transformers. Other vendors had an extremely
high failure rate of 35 kV bushings in the field, quality control wasn't
very good for others. I realized the problem was due to designs based
on transformer bushings - a completely different environment that switchgear.
Transformers are filled with oil, and are held in place by a front-mounted
clamp to allow field replacement. The oil covers up the back of the
bushing, insulating it. Switchgear used air on both sides. The lack
of oil allowed electrical stress and dust on the surface to create "tracking",
where the dust and moisture creates a conductive path. The skirts (those
ribs on the surface) create a longer path from the conductor to the
mounting plate. But diameter of the skirts was limited by the size of
the hole. I realized bushings could be mounted from the back, which
allowed me to use much larger skirts, and increase the diameter of the
body for more cantilever strength. Leakage distance doubled, and cantilever
strength was five-times higher - which eliminated the need for support
insulators, reduced the number of connections, lower cost and improved
reliability.
|
 |
High Voltage Insulators - These are known as "Apparatus
Insulators" in the Electric Power Industry. They use the same skirt
design and production methods as the bushings above. The size is designed
to exactly match the bushing, making it easier for an manufacturer to
design his products. One line is designed to be interchangeable with
a bushing, allowing a to reduce the number of switchgear designs. Their
performance in contaminated conditions, and our ability to rapidly design,
tool, and produce custom designs allowed us to enter the world-wide
OEM market. Taiwan became our largest customer. Our use of CAD, innovative
tooling and M4 manufacturing cut our time-to-market to 6 weeks, while
competitors usually took 6 months.
|
 |
Molding Press - A Liquid-Resin-Injection Molding Press I designed
in 1981 for molding cycloaliphatic epoxy bushings. Another "impossible"
project, ahead of schedule, under budget. You could buy one for $500,000
to $1,000,000 that would run 2-3 times faster. I built three for about
$12,000 each. A tool and die maker quoted $60,000 for one mold. I designed
my own and had them cut at a machine shop for about $4,500 each. The
expensive presses have noisy hydraulic pumps that run all day. This
press uses pneumatics, and make no noise, except when you open or close
them. I hate a noisy workplace.
|
 |
Enclosure Welding Jig - This is an adjustable jig for welding
Pad-Mount Switchgear Enclosures designed in 2003. It replaced 96 jigs,
and saved quite a bit of storage space. Although it weighs over 700
lbs, it can be easily rolled around the shop. I designed it, cut the
parts, did some of the welding (not much - my welds are ugly), created
and cut all the lettering. Most surfaces are covered in non-slip material
to allow the welders to climb all over it, which cuts the process time
and improves safety. The jig is designed so only standard-size enclosure
components will fit. This means that an incorrectly-cut part will not
fit, improving quality without the need to add a QC check. It doesn't
look like much, but it actually has a lot of little details that were
a huge improvement over the previous jigs, and produces a better product
through better alignment. There was a lot of attention paid to eliminate
the possibility of a worker cutting himself on any sharp edges.
|
MasterCost Software - In 1983, I developed a bill-of-materials
system that printed price sheets. It consisted of over 25,000 lines
of Basic code, developed over a 4 week period. The first software we
used took 26-28 hours to print a set of price sheets - the Apple III
computer couldn't keep up with a really slow NEC SpinWriter printer.
MasterCost did it in 1.5 hours on a laser printer. It allowed us to
enter new material costs and get new price sheets that same day. Working
30 hour days, I was so burned out on that project, I didn't write any
more code for 5 years. It ran on a Compaq PC (8 MHz) and MS-DOS 2.0.
|
CAD/CAM Networks - I started CAD Masters, a CAD/CAM/Network
dealership in 1990. We sold AutoCAD, MicroStation, SolidWorks, ESRI,
Intergraph, and HP products. We were a top dealer for Vidar large format
scanners and were the only Mutoh-authorized service dealer in Louisiana.
Customers included Boeing, Lockheed, Sunbeam, and many small manufacturers,
engineers and architects.
|
 |
Writing - I started writing reviews of high-end graphics boards
for Cadence magazine - an AutoCAD user magazine. Later, I wrote product
reviews for Cadalyst and wrote a monthly column on CAD for Plastics
Design Forum Magazine. PDFM closed, so that ended my magazine writing.
|
 |
Publishing - At CAD Masters, I was publishing a newsletter
that was mailed to over 16,000 users all over the United States. I started
creating catalog literature at Elliott Industries using a paste-up board
(hard work). At Elliott Molding and Components, I used PageMaker and
Ventura Publisher when they first came out. At CAD Masters, I started
using PhotoShop and Adobe Illustrator. I've used Quark Express, but
I'm not all that crazy about it.
I've become a big fan of Adobe products because they allow easy exchange
of files, generate clean EPS, and Acrobat files.
|
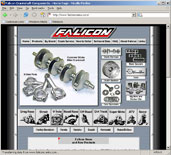 |
Web Sites - At CAD Masters, I was publishing a newsletter that
was mailed to over 16,000 users all over the United States. When the
Internet became popular, I switched to a web site. I began to develop
sites for other customers, including Meridian Therapies, Oxner Engineering,
Team LaSport, and Elliott Industries. I closed CAD Masters in 1999 and
went to work for Elliott Industries, and Technology Manager. Most of
the web sites I've built are no longer in existence.
Here's a web site I built
for Falicon Crankshaft Components. I did a lot (but not all) the product photography, all the photo editing (Photoshop), and the entire design/layout/artwork (except the original logo).
|
What's next? - I'm currently honing my skills using Macromedia's
new web development tools (Dreamweaver MX, Flash MX and Fireworks MX)
and Microsoft Visual Studio .Net (VB.Net and C#).
My first love is motorcycles, so I moved to Clearwater, Florida to
be closer to race tracks (Daytona, Sebring, and motocross). I worked
for Falicon Crankshaft for a while, then moved to the Daytona Beach
area and joined Homac Mfg. as a Product Design Engineer in the Research
and Development Group.
I'm convinced today's motorcycles are stuck in
conventional thinking. Why are downhill mountain bikes that run 60-70
mph carrying 180 lb. rider able to weigh only 35 lbs, yet have the
same suspension travel as 80's motocross motorcycles? Today's motocross
bikes are considered light when they weigh 196 lbs dry, yet Roger
DeCoster's 1972 Suzuki RH500 only weighed 160 lbs. Material science
has progressed, but it doesn't seem to have been applied. I had hoped
Cannondale's entry in motocross would have given us sub-100 lb motocross
machines, but they mimicked the existing players and went broke.
I also believe a lot of riders who are just getting into motorcycles
will become unhappy with their cruisers, and look for more performance-oriented
bikes. The industry is stuck in their thinking and don't understand
American riders. There's not much choice in American motorcycles and
I think its time for that to change.
Ken ///
My Resume
|
|